Adopting logistics technology can save up to 61% in operational time and reduce costs by 17%, but companies face seven key barriers.
Here’s a quick rundown of the challenges and how to tackle them:
- High Costs: Initial software, training, and operational adjustments can be expensive.
- Employee Pushback: Resistance from staff and management due to fears of disruption or job loss.
- Skills Gaps: Lack of digital literacy, data analytics skills, and system integration knowledge.
- Legacy Systems: Outdated infrastructure complicates integration with modern tools.
- Data Security Risks: Increased vulnerabilities with interconnected systems.
- Scaling Issues: Manual processes and limited integration tools hinder growth.
- Lack of Standards: Inconsistent protocols across the industry create inefficiencies.
1. High Implementation Costs
Adopting new logistics technology can be a heavy financial lift for many companies, involving both upfront expenses and hidden costs tied to operations.
There are three key areas where costs typically arise:
- Software & Infrastructure Costs: These include expenses like enterprise software licenses, hardware upgrades, system integration, and ongoing maintenance fees.
- Training & Staffing Expenses: Companies often face costs for staff training programs, a dip in productivity during the transition, hiring specialized IT personnel, and managing organizational changes.
- Operational Adjustments: Adjusting operations can involve redesigning processes, migrating data, handling system downtime, and updating documentation.
David Mateos from Cotransa Group‘s sales team shared his perspective:
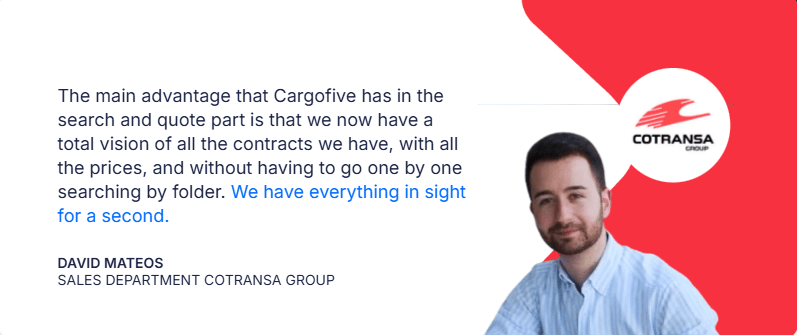
To manage costs effectively and ensure a good return on investment (ROI), companies can take practical steps like:
- Starting with essential features and expanding over time.
- Opting for platforms that already integrate with their existing systems.
- Using cloud-based solutions to reduce infrastructure expenses.
- Picking systems that are easy to use and require minimal training.
Although the financial commitment can feel overwhelming, tackling these costs is just the beginning.
Companies also need to prepare for potential resistance to change from employees and management.
2. Employee and Management Pushback
Resistance to change is one of the biggest challenges in adopting new logistics technology.
Both employees and management often worry about job security, workflow disruptions, and the complexity of new systems.
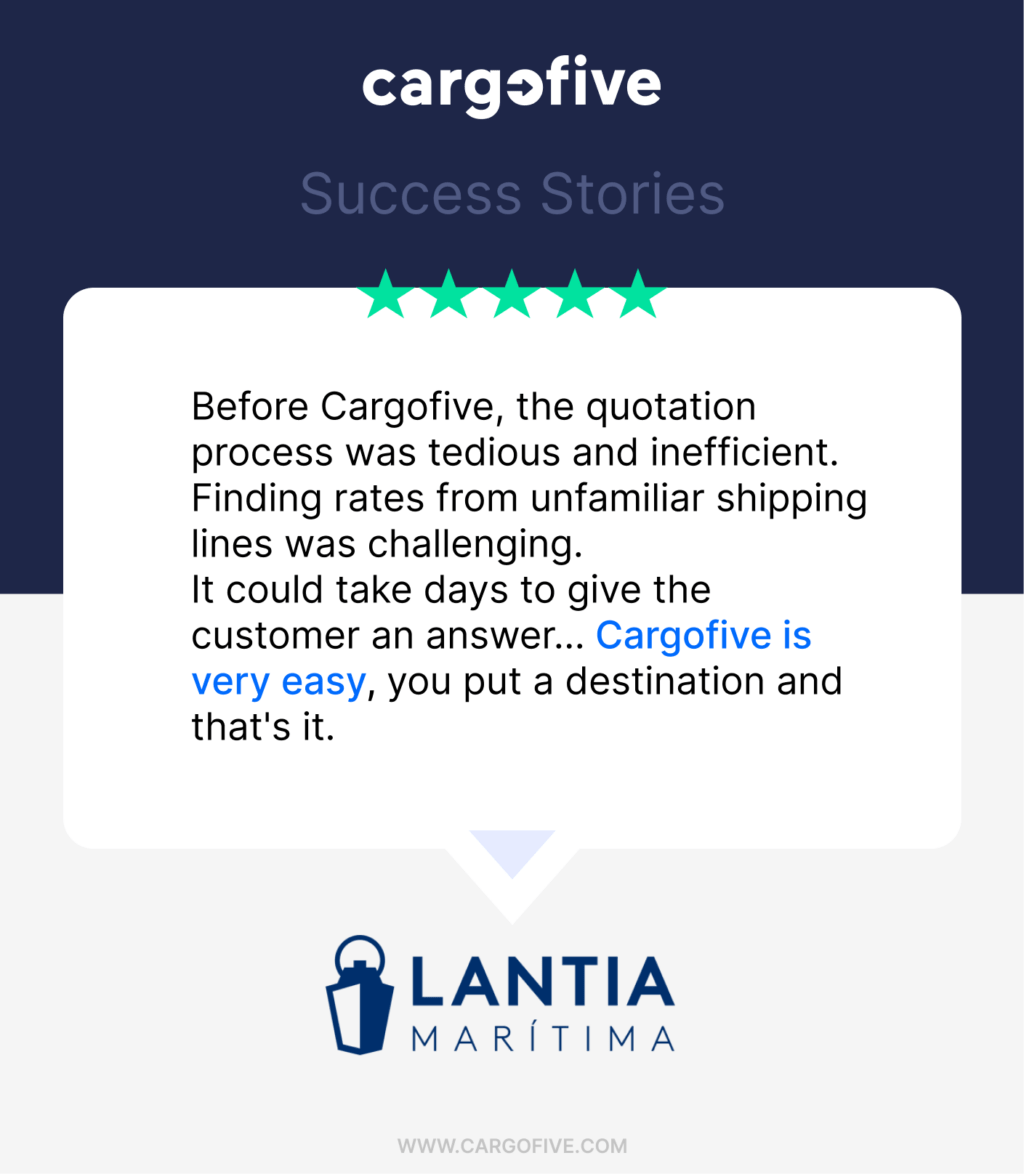
One major concern is the fear that automation will replace jobs.
However, many real-world examples show that technology often complements human work rather than eliminating it.
Here are the three main types of resistance that companies face:
- Operational Staff Concerns: Workers may feel anxious about steep learning curves or short-term drops in productivity during the transition.
- Middle Management Hesitation: Managers often worry about disrupting established workflows and hitting performance targets while adapting to new systems.
- Executive Leadership Skepticism: Senior leaders might question whether the investment will pay off and fear potential risks to existing client relationships.
To address these issues, businesses focus on strategies like gradual rollouts to minimize disruptions, clear communication about the process, and thorough training programs to build confidence. By managing the transition carefully and showing the benefits of new systems, companies can ease resistance and encourage buy-in.
Next, let’s explore how skills and training gaps create additional challenges in adopting technology.
3. Skills and Training Gaps
The logistics industry is grappling with a tough challenge: moving from traditional methods to modern technology.
A major hurdle? The lack of workers skilled in both operational and tech-based roles.
This gap is slowing down the adoption of new systems and processes, especially in some key areas.
Here are the main gaps causing issues:
- Digital Literacy: Many seasoned professionals are great at traditional operations but struggle with the digital tools now essential for the job.
- Data Analytics: Teams often find it hard to interpret and use the massive amounts of data generated by new technologies.
- System Integration: Employees frequently lack the know-how to connect new solutions with older, existing systems.
To tackle these gaps, companies must prioritize building internal expertise.
This means going beyond just addressing costs or resistance to change.
Training efforts should cover basic technical skills, advanced system capabilities, and how to integrate new tools with existing infrastructure.
Some practical steps businesses can take include:
- Designing role-specific training programs tied to the actual tasks employees perform daily.
- Offering ongoing learning opportunities to keep up with evolving systems.
- Setting up peer mentoring programs to encourage knowledge-sharing among team members.
- Providing clear documentation and quick-reference materials for easy access to key information.
Investing in training and support systems isn’t optional – it’s necessary for successful tech adoption.
Up next, we’ll dive into how legacy systems add another layer of complexity to this process.
4. Legacy System Compatibility Issues
When companies plan upgrades, dealing with older systems often complicates digital transitions.
For many logistics businesses, outdated systems remain a major hurdle to adopting new technologies.
This highlights the importance of having a clear modernization strategy.
The main issue lies in connecting modern technology with older infrastructure.
Logistics companies typically work with a mix of systems, including:
- Older Enterprise Resource Planning (ERP) systems
- Transportation Management Systems (TMS) built on outdated platforms
- Custom-built software solutions
- Paper-based or non-digitized workflows
This patchwork of systems leads to several challenges:
- Data format conflicts: Modern systems use standardized APIs, while older systems rely on proprietary formats. This mismatch can cause translation errors or even data loss.
- Real-time issues: Legacy systems often lack real-time data exchange capabilities, leading to delays and inconsistencies.
- Security risks: Outdated systems are more vulnerable to breaches due to the lack of modern safeguards.
To tackle these problems, a strategic, phased approach works best.
Start by auditing current systems to identify critical integration points. Middleware or API layers can help bridge the gap between old and new systems.
It’s also smart to prioritize tools with strong integration capabilities.
For example, platforms like Cargofive simplify freight management and cut costs. The goal is to adopt solutions that allow for smooth modernization while keeping operations running smoothly.
5. Data Security Risks
As supply chains become more interconnected, the risk of data breaches grows.
Legacy systems only add to the challenge, making the shift to digital operations even more complex.
Logistics companies handle highly sensitive information, including customer shipping details, payment data, pricing strategies, carrier agreements, and operational metrics like real-time tracking and inventory levels. This makes them a prime target for cyber threats.
The rise of digital tools such as cloud platforms and IoT devices has introduced new vulnerabilities.
Common risks include unsecured APIs, mobile device threats, third-party access loopholes, and poorly configured cloud storage systems.
Ignoring these risks can lead to financial losses, operational downtime, reputational harm, and legal consequences.
To safeguard critical data, companies must adopt strong security measures and carefully vet their technology solutions.
These vulnerabilities also pose challenges to scaling operations and adapting to new demands.
6. Growth and Scaling Challenges
Technology constraints can hold back a logistics company’s ability to grow and scale effectively.
Addressing these challenges is just as important as managing costs and overcoming resistance in today’s competitive logistics world.
Freight forwarders often lose valuable time manually processing rates and comparing carrier options, creating bottlenecks that slow operations and limit growth opportunities.
These inefficiencies are tied to a lack of real-time operations and integration tools, which are critical for scaling.
When companies don’t have instant access to updated pricing and capacity data, making quick, expansion-focused decisions becomes a struggle.
This reliance on outdated systems and manual processes only adds to inefficiencies.
The problem becomes even more pronounced when businesses operate across different regions or time zones.
As companies grow, another hurdle emerges: integrating various systems. Each new integration demands resources and expertise, which can delay expansion plans.
Without automation, companies face severe limitations in their ability to grow.
Here are some common challenges and their impact on scaling:
Challenge | Impact on Scaling |
---|---|
Manual Rate Processing | Slower responses to market demands |
Limited System Integration | Difficulty onboarding new partners |
Lack of Real-time Visibility | Delayed decisions and planning |
Format Discrepancies | Higher error rates during growth |
Overcoming these challenges can lead to major improvements.
For example, companies that invest in advanced tools and automation have reported up to 61% time savings and a 17% reduction in overall operational costs.
7. Lack of Industry Standards
One of the biggest obstacles to adopting logistics technology is the absence of unified standards.
Much like the challenges of dealing with outdated systems, inconsistent protocols make system integration unnecessarily complex.
This fragmentation means carriers, freight forwarders, and vendors often rely on different formats and systems.
For example, freight forwarders face inefficiencies when managing rates across multiple carriers, each using its own unique standards.
This not only complicates processes but also drives up costs.
Creating common frameworks could help solve these problems. While there are ongoing efforts to establish standardized protocols, achieving widespread use has proven difficult.
Platforms like Cargofive offer a glimpse of how technology can help bridge the gap.
Designed to simplify freight rate management and integrate with major shipping lines and ERP/TMS systems, tools like this provide partial solutions.
However, without industry-wide standardization, businesses will continue to face challenges in optimizing their operations.
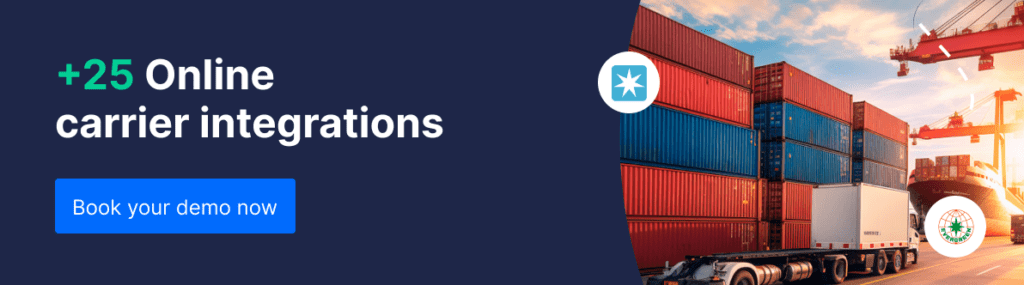
Conclusion
While the logistics industry faces numerous challenges in adopting new technology, these obstacles can be tackled with the right approach.
Issues like cost, resistance to change, skill shortages, outdated systems, data security concerns, scalability, and aligning with industry standards all play a role, but addressing them paves the way for meaningful transformation. Companies that embrace digital tools often see improved operations and noticeable cost savings.
To move forward, businesses should take a thoughtful approach. Start by analyzing current technological needs and creating a clear plan.
This plan should include reviewing existing systems, pinpointing integration needs, and rolling out thorough training programs.
Experts in the field highlight how automation simplifies rate comparisons and boosts visibility, leading to impressive efficiency improvements.
AUTHOR